I. Introduction | Second, the principle of EtherCAT technology | 3. Implementation of EtherCAT | 4. Conclusion and Prospect |
Industrial Ethernet technology is a research hotspot in the industrial control industry. EtherCAT technology is gaining more and more attention from the R & D personnel due to its high speed, simplicity and ease of implementation. This article introduces the principle and protocol form of EtherCAT technology in detail, and gives a specific EtherCAT slave implementation method in combination with TMS320LF2407.
[Keywords] Industrial Ethernet, EtherCAT, TMS320LF2407.
The principle of Industry Ethernet-EtherCAT
and its implementaTIon
WANG Wei-jian
(Research Center of Shang Hai Xin Hua Control Technology Group Co. Ltd)
Industry Ethernet is becoming researching hot. EtherCAT as a kind of industry Ethernet is getTIng much more attenTIon with its high speed, simplicity and easy availability. This paper introduces the principle of EtherCAT and its protocol, in addiTIon, this paper tells how to implement EtherCAT slave with TMS320LF2407.
Key words Industry Ethernet, EtherCAT, TMS320LF2407.
1. Introduction Fieldbuses have been the mainstream solution for field-level communication systems in the fields of factory automation and process automation in the past decade. However, with the continuous progress and development of automated control systems, traditional fieldbus technology has been difficult to meet the growing needs of users in many applications. Ethernet has achieved great success on the local area network and the Internet. In the entire enterprise information system, Ethernet has been very successfully applied to market management, production management and process monitoring layer. If Ethernet can be introduced into the underlying device network, it can not only facilitate the vertical integration of the field device layer, process control layer and management layer, but also reduce the integration cost of different manufacturers' devices at the horizontal level.
At present, industrial Ethernet technology has become a research hotspot in the field of industrial control, and many automation companies have launched their own industrial Ethernet solutions. At present, the main industrial Ethernet standards are as follows: Modbus / TCP, EtherNet / IP, Profinet, Powerlink, EtherCAT, and EPA developed in China. Compared with the traditional control network, industrial Ethernet has many advantages such as wide application, support by all programming languages, abundant software and hardware resources, easy connection with the Internet, and seamless connection between the office automation network and the industrial control network.
EtherCAT (Ethernet for Control Automation Technology) is an industrial Ethernet technology developed by German automation company Beckhoff. The technology is gaining more and more attention from product developers due to its high speed, simplicity and ease of implementation. At the end of 2003, ETG (Ethernet Technology Group) was established, responsible for the promotion and publicity of EtherCAT technology. At present, the organization currently has more than 700 members, and many member organizations have developed products based on EtherCAT.
Second, the principle of EtherCAT technology
EtherCAT is a real-time Ethernet fieldbus system. This protocol can be used to optimize the transmission of process data. The EtherCAT protocol can include several EtherCAT messages, each of which serves a specific memory area of ​​a logical process image area, which can be up to 4GB bytes. The order of data to be sent and received does not depend on the physical order of the Ethernet terminals in the network, and can be arbitrarily addressed.
As a real-time Ethernet protocol, the OSI model of the EtherCAT slave can be described simply using Figure 1. In Figure 1, the seven-layer OSI model of open system interconnection defined by ISO International Standards Organization is compressed into a three-layer model with physical layer, data link layer and application layer. The physical layer provides a physical link for the transmission of network signals. The main task of the data link layer is to extract data from the Ethernet frame within a specific "time window" and insert the data to be output into the Ethernet frame, while checking and verifying the data. If the action cannot be completed within a certain time window, the action is considered to have failed. The role of the application layer is to process requests from the data link layer and respond appropriately.
Figure 1 EtherCAT OSI model
The EtherCAT protocol itself determines that it does not need to receive Ethernet data packets, decode them, and then copy the process data to each device. It has the principle of master-slave data exchange and requires the master station and slave stations to cooperate to complete the work. Therefore, EtherCAT is very suitable for communication between the master and slave controllers. The Ethernet frame transmitted by the EtherCAT master station contains all the I / O slave station data. The message is transmitted between the I / O slave stations. Each slave station takes a very short time to obtain data and write the data to be sent to the Ethernet The corresponding position of the network frame, and then pass the message to the next slave station. After the last slave has been processed, the message is passed back to the EtherCAT master.
The EtherCAT protocol structure is shown in Figure 2. Figure 2 shows that due to the large amount of device data compressed by the Ethernet frames sent and received, EtherCAT fully utilizes the bandwidth of the IO layer and uses the EtherCAT protocol for data transmission. The available data transmission rate can reach more than 90%, 100 Mbit / s The full-duplex feature of is fully utilized. According to some data, it takes only 30 microseconds to process 1000 digital I / Os and 50 microseconds to process 200 16-bit analog signals, that is, the sampling frequency reaches 20 kHz. This real-time Ethernet protocol is very suitable for applications that require fast control. It can really apply Ethernet to the sensor / actuator level. The EtherCAT protocol itself determines that it supports almost any topology type, including line, tree, star, etc., and is not limited to the number of cascade switches or hubs.
In terms of fault diagnosis, EtherCAT can effectively detect bit failures during data transmission through CRC check, and EtherCAT can perform wire break detection and fault location through matching check. In addition, the protocol of the EtherCAT system can also separately monitor the quality of each transmission segment, and the automatic evaluation associated with the error counter can also accurately locate the critical network segment.
3. Implementation of EtherCAT
The realization of EtherCAT technology includes master station realization and slave station realization. The EtherCat master station does not require a dedicated communication processor, it only needs to use a passive NIC card or an integrated Ethernet MAC device on the motherboard, and completely uses software to achieve protocol identification and packaging in the host CPU. EtherCat can achieve up to 1486 bytes of distributed process data communication in a single Ethernet frame. In order to facilitate the development of the master station, the EtherCat organization now provides the master station sample code, which can be easily embedded into the real-time operating system to speed up the project development process. The man-machine interface of the EtherCAT master station used in this article is shown in Figure 3.
Figure 3 Test EtherCAT master station man-machine interface
EtherCat slaves are implemented with dedicated hardware. Currently, many manufacturers provide EtherCAT slave controllers, and they can also purchase authorized binary codes at once, and realize the functions of slave controllers through low-cost FPGAs. The dedicated hardware to realize the slave station has two MAC addresses, which can easily expand the two network ports. The purpose is to facilitate cascading and form various topological structures.
This article uses TI's 16-bit processor TMS320LF2407 as a microprocessor and Beckhoff's ET1100 as an industrial Ethernet Ethercat protocol communication controller. TMS320LF2407 implements the application layer of the EtherCat protocol, and can access data to the DPRAM inside the ET1100 through a 16-bit parallel port. ET1100 has two MII interfaces, which implement the data link layer of the EtherCat protocol on the hardware, and the two extended physical layer chips implement the physical layer of industrial Ethernet. The role of the network transformer is to achieve isolation and impedance matching. The data communication rate between the master station PC and the slave station reaches 100Mbit / s. The specific block diagram of the slave station is shown in Figure 4.
Figure 4 Block diagram of the slave station
4. Conclusions and Prospects As an industrial automation Ethernet solution, EtherCAT is gaining the favor of more and more R & D personnel due to its high speed, simplicity, and ease of implementation. Many manufacturers have developed their own master station products and As for the station chip, many domestic manufacturers have begun to focus on the product development of this technology. Xinhua Group R & D Center has taken the lead in realizing the productization of EtherCAT technology in China, successfully developed the first set of EtherCAT-based DCS TisNet-E1000 in China, and has led the development of automation products based on EtherCAT technology in China.
The author's innovative point: Based on the 16-bit processors TMS320LF2407 and ET100, EtherCAT slave stations are implemented, and the EtherCAT technology verification platform is built, leading the productization of EtherCAT technology in China.
references
[1] Cui Yan Wang Qianping Ma Haibo FPGA-based Industrial Ethernet Flexible Solution Microcomputer Information, 2009, 2-2: p167-p169
[2] Chen Weimin and Xie Nan develop microcomputer information based on ARM-based industrial Ethernet intelligent gateway, 2008, 2-2: p133-p134
The new product line is the characteristic product of our company's production and development, mainly including the Anti-corrosive Aluminum alloy spinning lamp pole,Solar Camera light,Cylindrical Intelligent Street Lamp,No power LED Module .
1.Aluminum alloy spinning lamp pole
The spinning pole is the use of foreign advanced spinning equipment,forming a whole without welding,forming a conical or profiled bar.And then polishing,remove surface oil,burr and indentation.Then after the quenching intensity,to T6 state,in line with international standards.The product never rust ,strong corrosion resistance,diversified surface treatment process,the appearance of simple fluid lines.Light weight and convenient installation and transportation,the rod body can be 100%recycling,low melting temperature.
Product features
â‘ Using spinning equipment advanced,the whole forming a non welding
â‘¡Product permanent does not rust,corrosion resistance
â‘¢Diversified surface treatment technology,make the appearance line succinct smooth
â‘£The light weight,convenient installation and transportation
⑤The rod body can be 100% recycling,melting temperature is low.
2.Camera street light
The camera street light is used to use the infrared network high definition intelligent ball's various features so that it can be widely used in the need of large-scale hd quality control of the site.
Functional properties
â‘ Smart Function:Smart Tracing,Smart Inspecting,Smart Road Monitor
â‘¡System Function:Smart Video,Smart Photo Enhancement
â‘¢Movement Function
â‘£Network Function
3.Intelligent Street Lamp
Intelligent Street Lamps are also called intelligent lighting or smart street lights.It adopts the Internet of things and cloud computing technology to comprehensively upgrade the urban public lighting management system, so as to realize centralized control, operation and maintenance information and intelligent lighting of street lamps.The most advanced versions of Intelligent Street Lamps have been designed to create a happy atmosphere in roads, streets, squares and other places.The design of intelligent street lamps can only be designed by a wide range of discussions and environments that provide an aesthetic consistency.
Product feature
1.Sensor
Monitoring urban environment conditions
Sensor norise
Air pollution sensor
Temperature/humidity sensor
Brightness sensor
Municipal construction monitor
2.RFID
Special crowed monitor
CMC monitor
Community security monitor
Municipal facilities monitor
3.Communication Services
Micro base station
Street lights embedded WIFI hot spot
4.Video Monitor
Security monitor
Vehicle monitor
5.Emergency Broadcast
Active of the external field radio monitoring center
6.Intelligent Lighting
Cellular cooling technology
Based on the luminance uniformity of light distribution
Intelligent single lamp/center controller
Variety of modular design lamp,holder is optional.
7.Information Release
Advertising exposure
Current politics news
Information release
8.Charging Column
Electric car
Electric bicycle
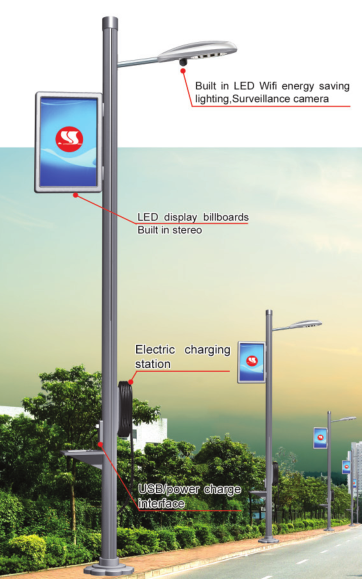
4. Led Module
â— The unique acicular radiator,360 degree dissipation small wind resistance. High heat dissipation efficiency ensuring that the LED chip can work for 50000 hours.â— Color temperature 3000-6000K
◠Light≥90LM/W
â— Matching the 2.3.4 lane,tunnel and Landscape Lamp,floodlight dedicated lens.Ensure that intensity and uniformity.
â— Glare index Signification reduce the original LED module size,removal of power supply problems.Low demands for application situation and installation personnel .More suitable for the transformation of traditional lamps.
Product features
â‘ The solid heat conduction,Plug-in package technology
â‘¡Alternating current method,Alternating current direct drive to overturn the traditional application.
â‘¢Avoid long-distance power.Transfer will have excess loss.
â‘£No power supply ACLED
⑤Customized LED lens
â‘¥Automatic dimming system intelligent.
⑦Wide application,flexible combination.
Aluminum Alloy Spinning Lighting Pole,Lightest Aluminum Alloy,Aluminum Alloy Torchlight,Lightweight Aluminum Alloy
Jiangsu chengxu Electric Group Co., Ltd , http://www.chengxulighting.com